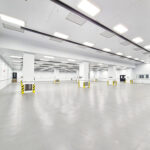
The increasing financial pressure from the global economy is having some devastating results within the industry with many choosing to move to lower cost centers, mothball their assets and restart when market conditions improve, or selling sites for development or demolition.
Why is understanding and managing demolition so important?
One of the most frequently asked questions I get asked is: “Isn’t demolition just construction in reverse?”, to which the answer is no and in fact, nothing could be further from the truth.
In construction, once the foundations of a structure are installed you then begin putting the pieces of a jigsaw together, whereas for decommissioning and demolition there are many unknown potential hazards and risks that need to be constantly managed.
Often when an asset is no longer required it will be decommissioned and mothballed which may seem like the right thing to do. However, in most cases this creates unnecessary risk where relevant and accurate information may not be recorded or lost meaning the demolition contractor will be going into the project “blind”.
The Challenges
The offshore decommissioning process is often restricted due to access issues caused by structures still being occupied, still energized/operational or being too remote.
To achieve optimum success, planning for demolition should begin three to five years before the potential Cessation of Production (COP) date, although this can be difficult to do because not all COP dates are known at this point.
Where possible however, it is imperative to give enough time to ensure that the project is legally compliant.
For example, if the project requires transportation for redundant structures to a UK disposal yard, there must be considerations given to the UK regulatory framework and trans-boundary regulations.
The Construction (Design and Management) Regulations (CDM) 2015 need to be complied with on all projects of this type. This regulation is derivative of the 92/57/EEC European Directive resulting in similar requirements for some European disposal yards.
Under the CDM Regulations, the operator has a responsibility as the Duty Holder to ensure all Duty Holders have access to the relevant information and follow the “Principles of Prevention” to manage and remove the foreseeable risks through design.
The CDM (2015) regulations place specific responsibilities on key Duty Holders i.e. Clients, Principal Designer’s and Principal Contractors.
These roles need to be formally appointed by the client in writing, failure to do so will result in the client taking on the roles and duties by default.
The Principal Designer needs to be appointed at conception stage to allow for time to ensure the “design” considers principals mentioned above.
Onshore experience has shown that an asset can become unsafe to decommission when it is left in a “cold and dark” state for too long due to deterioration and when the asset is in a hostile environment for example offshore/exposed location, the rate of deterioration can increase significantly.
This may prevent safe access to the asset significantly increasing the risks to the removal team and greatly increase the potential for loss of containment for which the results are extremely detrimental to the environment.
What is the “Designing for Demolition” concept?
ABB has developed a concept to move from a state of unknown to a known state to reduce the risks during the demolition process which gives improved commercial results for our clients while continuing to ensure safety, environmental protection and legal compliance during the demolition process.
Organizations are very skillful at asset management and maintenance, however for a lot of them decommissioning and demolition are still very much unchartered waters.
The basic principal is to carry out as much work as possible onshore and minimize decommissioning work offshore, this is done to allow transporting of redundant structures to the final disposal location.
This process can begin with a HazDem Study during the Late Life stage of the asset lifecycle to identify the scope of work needed in preparation for COP and decommissioning of the asset.
As mentioned above studies offshore are restricted and tend to be incomplete due to those restrictions.
We have a saying in the industry that “we believe everything you tell us but we believe nothing”, this will result in the studies being carried out when the structure arrives at its final disposal location.
The consequences of this are that extra decommissioning works which will be required before any demolition project can begin, and on some occasions, this will in the client to paying twice.
Done correctly this will greatly reduce variations.
These principals are important whether the decommissioning is onshore or offshore.
Ultimately, by successfully “Designing for Demolition” you can greatly reduce the risks to people, environment, costs, programme and reputation.
So, ask yourself, could any of your previous projects of this type have reaped the benefits of the ABB “Designing for Demolition” concept?
By Steve Andrew
By ABB Limited
1580 Views