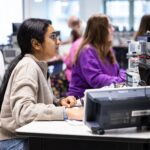
UK-based contamination control experts the Guardtech Group have a long history of turning tired, old premises into stunning new homes for a wide range of applications
CONSTRUCTING new cleanroom facilities in older buildings can be a smart and cost-effective solution for applications looking to optimise their existing spaces.
Rather than invest in completely new host buildings, it is often possible to intelligently and creatively adapt current facilities, saving both time and money. However, this approach comes with its own set of challenges.
Many older buildings have structural limitations that can impact load-bearing capacity, electrical systems, ceiling height and ventilation. Addressing these issues requires careful planning and a flexible design approach.
“We do as much as we can to work collaboratively with our clients,” says Guardtech Group Commercial Director Mark Wheeler. “But there are occasions when we need to let our expertise and knowhow guide the planning stages.
“We’ve dealt with enough tired, old facilities over the years to know the potential pitfalls and common difficulties. Which also means, in turn, that we have a wealth of ideas and solutions to help overcome any major stumbling blocks.”
The Guardtech Group have extensive experience when it comes to redeveloping older host buildings, with a wide-ranging back catalogue of projects across Life Sciences and High-Tech Engineering including a recent complex controlled environment refurb for global innovators GKN Aerospace in East Cowes in the United Kingdom.
In that instance, Guardtech delivered a 1,650sqm cleanroom within a warehouse that was more than 100 years old.
To ensure the cleanroom fit within the existing structure, the building was first scanned using state-of-the-art 3D Lidar Scan technology.
Since the structure could not support additional weight, Guardtech – through their large-scale turnkey brand Cleanroom Solutions – constructed a separate steel framework from which to hang the ceiling and modular panels that make up the internal structure.
Another common challenge is how to integrate new and existing installations. Older facilities may already have electrical trays, a sprinkler system, ventilation ducts and gas lines.
Guardtech utilise the best software on the market, such as Autodesk Construction Cloud, to ensure that all these elements are incorporated into any new design to avoid clashes.
In many cases, separate HVAC systems are also installed, as cleanrooms require more stringent control of humidity, temperature, and air exchange than the existing building can typically provide.
And that’s not where the challenges end, as Guardtech Nordic AB Director Lars Strandljung can testify.
“When it comes to height limitations, optimising the cleanroom ceiling design is crucial to ensure sufficient plenum space for filtration systems,” he adds.
“By customising the ceiling height, Guardtech can create an optimal environment without compromising cleanroom performance.
“Leveraging existing buildings is often the most economical option. If a facility is already available, it makes sense to utilise it. This also help to avoid those nasty, lengthy lead times you associate with new construction, such as decision-making, permits and building schedules.”
But what if it’s not possible to adapt the current space? Perhaps there are planning restrictions in your way – or you cannot obtain the permission of the host building’s landlord?
Maybe time or budget is compromised – or you simply cannot afford to suffer the hassle that a lengthy on-site construction project brings?
In such cases, Guardtech offer an innovative solution in the form of Cleancube Mobile Cleanrooms. This pre-fabricated cleanroom solution is built within shipping containers and can be placed in a warehouse, parking lot or simply on a concrete slab.
Cleancube is a rapid, plug-and-play solution, typically requiring only an electrical connection to be fully operational.
Modules can be custom designed in collaboration with the client to meet specific needs. Guardtech’s Multi system allows applications to conjoin as many 40ft containers together side by side to create whatever footprint they require.
But they’re now taking that award-winning concept to new levels, literally, with their Maxi system – which gives clients the option to stack as many modules as they wish on top of another to create even larger shipping container facilities.
Strandljung says: “Rather than risk a long period of critical downtime while a turnkey construction project takes place, Cleancube container cleanroom modules can be constructed at Guardtech’s UK manufacturing facility, dropped into a car park or warehouse space and ‘stitched together’, ready for immediate plug-and-play deployment all over the world.
“Equally, if a full-scale refurb of an existing facility is still required, Cleancube container cleanrooms offer an ideal short-term solution into which businesses can temporarily move their production until a newly constructed host building is complete.”
“It’s an ideal solution,” adds Wheeler. “There’s no need for all the disruption a construction site brings – these modules are pre-fabricated and delivered to site, keeping hassle to a minimum whilst ensuring all the benefits of a world-class modular cleanroom remain true.”
By combining a wealth of experience, innovative solutions and flexibility, Guardtech help companies create optimal cleanroom environments, regardless of the challenges that older buildings may present.
For more information on Cleancube Mobile Cleanrooms, email sales@guardtech.com or visit www.cleancube.co.uk. For more on the Guardtech Group, visit www.guardtechgroup.com.
By Guardtech Group
31 Views