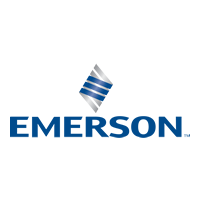
Rethinking Flow Measurement for Hydrogen Gas:
Flow measurement plays a critical role in industrial processes, particularly in the chemical industry, where accuracy and safety are paramount. Traditional flow measurement methods often pose challenges when dealing with highly corrosive gases like hydrogen chloride (HCl). To overcome these difficulties, clamp-on ultrasonic flow measurement has emerged as a non-intrusive, efficient, and safer alternative.
Overcoming the Challenges of HCI Gas Flow Measurement:
Hydrochloric acid is a fundamental chemical used across multiple industries, from ore processing to pharmaceuticals. Its production involves the absorption of hydrogen chloride gas into water, with precise control over the gas and water flow rates being essential to achieving the target concentration of 38% HCl.
At an industrial site producing high-purity hydrochloric acid, the flow of HCl gas into an absorption column was traditionally measured using a differential pressure-based flow meter. However, this method presented several challenges:
• Low Pressure: The HCl gas had low pressure, making traditional differential pressure-based flow measurement challenging.
• Corrosive Nature: The gas’s high corrosiveness necessitated plastic pipelines and specialised equipment.
• Complex Maintenance: The previous system required two shut-off valves for maintenance, demanding extensive protective measures, including full breathing apparatus for personnel.
In the pursuit of enhanced plant safety and operational efficiency, engineers sought an alternative measurement solution.
Clamp-On Ultrasonic Flow Measurement:
Non-intrusive clamp-on ultrasonic flow measurement technology provided a simple yet highly effective option. This method operates by transmitting ultrasonic signals through the pipe walls and analysing their interaction with the gas flow inside. Since there is no direct contact with the medium, maintenance issues are reduced.
Given the low-pressure conditions of HCl gas, initial scepticism surrounded the feasibility of ultrasonic measurement. However, a four-week trial demonstrated that the technology could reliably and accurately measure gas flow under these conditions. The success was largely attributed to the acoustic properties of the plastic piping, which facilitated effective ultrasonic signal transmission even at atmospheric or negative pressure.
Improved Safety and Operational Benefits:
The adoption of clamp-on ultrasonic flow measurement delivered several key advantages:
• Enhanced Safety: Eliminating invasive components reduced exposure risks, improving workplace safety.
• Lower Maintenance Costs: No direct contact with the corrosive gas eliminated the need for frequent equipment replacement and complex maintenance procedures.
• Accurate Measurement Across All Operating States: Unlike pressure differential methods, ultrasonic technology provided consistent readings across varying flow rates, from system start-up to shutdown.
By leveraging clamp-on ultrasonic technology, plant engineers successfully improved both operational reliability and safety while maintaining precise control over hydrochloric acid production. This innovative approach exemplifies how modern measurement technologies can address industry challenges while enhancing efficiency and workplace safety.
To find out more about the capabilities of clamp-on ultrasonic flow measurement in the chemical industry, or to discuss short or long-term portable flowmeter rental options, contact Simon Millington – www.emerson.com | flexim-uk@emerson.com | +44 (0)1606 781 420
External URL: www.emerson.com
By FLEXIM Instruments UK Ltd
33 Views